The flange processing process differs depending on lathe and cutting, sheet metal drawing and bending. Here, we will explain the process of flange machining by drawing, using flanged cylinders as shown in the figure below as examples.
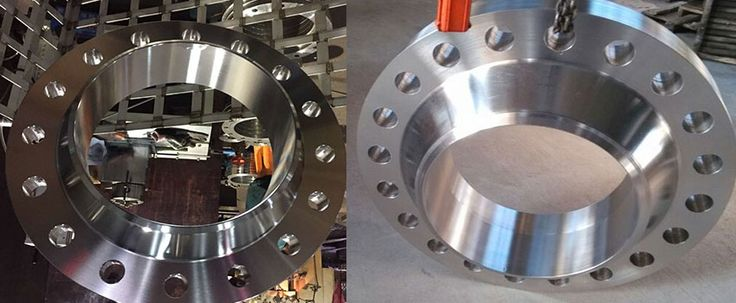
(1) Determination of dimensions
When forming a flanged cylinder, the finished shape of the product is first expanded to determine the dimensions of the blanks. However, in the drawing process, the edge of the flange deforms after molding, so it is necessary to determine the trimming fee.
Blank dimensions can be calculated using the flange diameter plus the trimming fee by the following formula.
Blank dimension formula
D=x2+4yh
D: Blank diameter, x: Flange diameter, y: Diameter of drawing part, h: Height of drawing part
This formula assumes that the plate thickness does not change after molding, and that the curved part is small. In addition, the diameter of the drawing part can be the inner diameter, outer diameter, or plate thickness center, but if you keep it as the outer diameter, the flange diameter will increase, so you can afford the trimming fee.
(2) Determination of the number of apertures
This blank is processed, but the drawing process usually cannot be molded to the finished shape in one time. That’s because there’s a limit to the depth you can squeeze. Therefore, we repeatedly squeeze the aperture process with a aperture diameter larger than the finished shape and a shallow drawing depth, while bringing the drawing diameter and drawing depth closer to the finished shape.
Calculating aperture diameter
The aperture diameter is calculated from the equation and value of the aperture rate considering the processing hardening of the material, referring to the relative plate thickness representing the ease of drawing.
Calculation method
- Aperture ratio = diameter after drawing ÷ diameter before drawing
- Relative plate thickness = plate thickness ÷ blank diameter ✕ 100 (%)
Aperture rate
- Initial aperture: 0.5 to 0.6
- 2 Aperture: 0.75 to 0.8
- After 3 aperture: 0.8 to 0.9
Relative plate thicknesses are less likely to be squeezed and larger. Therefore, if the relative plate thickness is small, the aperture rate is a large number, and if the relative plate thickness is large, the aperture ratio is a small number, and the diameter after drawing is calculated.
Calculating the number of apertures
When the aperture diameter is determined, the number of apertures can also be calculated. The drawing diameter at the time of each drawing is as follows.
Aperture diameter at each drawing
- Aperture diameter after the first squeeze … Blank diameter ✕ Initial aperture aperture rate
- 2 Aperture diameter after drawing … Aperture diameter after initial aperture ✕ 2 aperture ratio
- 3 Aperture diameter after drawing … 2 Aperture diameter after drawing ✕ 3 aperture ratio
The number of apertures you want is the number of apertures when this aperture diameter is smaller than the inner diameter of the aperture.
Calculating aperture height
The drawing height for each drawing process is determined from the blank diameter formula described above as follows:
The aperture height of each process
- h=(D2-x2)÷(4y)
- h: height of the drawing part, D: blank diameter, x: flange diameter, y: diameter of the drawing part of each process
This aperture height is used to determine how deep the punch is to be pushed into the blank in each process. However, it is only for reference only, and it is assumed that you look at the aperture state and adjust it.
(3) Mold design
Next, you will design the molds for each step of the drawing process: punches and dies.
Punch Design
The punch design determines the diameter of the punch and the shoulder radius.
The diameter of the punch is determined from the drawing diameter, taking into account the inner diameter of the molded shape.
If the flanged cylinder is measured as an example and the relative plate thickness is large, the punch diameter for each process is as shown below.
The shoulder radius of the punch is determined in turn from the shoulder radius of the completed shape to the shoulder radius of the final previous process, and so on, and so on.
First, as shown in the figure below, the center of the shoulder radius of the completed shape is the center of the shoulder radius of the final previous process. Next, the distance from the center of the shoulder radius to the end of the punch in the last two previous processes is divided into 3 to 4 equals, and the position slightly shifted to the end side of the punch is the center of the shoulder radius of the final two previous processes. Repeat to determine the shoulder radius of the initial aperture.
Also, be careful because the shoulder radius of the punch is too small to crack when machining, and if it is too large, wrinkles will occur.
Die Design
The die design determines the diameter of the die hole and the shoulder radius.
The hole diameter of the die cannot simply be the diameter of the punch plus the thickness of the plate. This is because with the drawing process, the edge of the cylinder shrinks and the plate thickness increases. Therefore, the hole diameter of the die of the first aperture is set so that the clearance is greater than the thickness of the plate. However, since the increase in plate thickness worsens dimensional accuracy, the clearance is brought closer to the original plate thickness as the drawing process progresses. In addition, for drawing near the final process, the clearance may be smaller than the original plate thickness, and the material may be squeezed to make the thickness uniform.
In the dimensions of a flanged cylinder as an example, the inner diameter of the die in each process is as shown in the figure below.
The shoulder radius of the die should be equal to or slightly larger than the shoulder radius of the punch in each process.
However, the boundary between the flange and the cylinder often does not have the appropriate dimensions. That’s because the blanks placed on the shoulders of the die are just held down with a blank holder and no punches are made. Therefore, we may perform a process called restrike to adjust the shape of this part.
(4) Selection of press machines
In the selection of press machines, it is necessary to calculate the drawing force for the selected material and select one that can demonstrate that power.
The following formulas are often used to calculate the drawing force of cylindrical apertures.
How to get the drawing force of cylindrical apertures
- P = K ✕ π ✕ d ✕ t ✕ Ts
- P: Drawing force (Kgf), K: Coefficient, π: Pi, d: Drawing diameter (mm), t: Plate thickness (mm), Ts: Tensile strength (Kgf)
Here, coefficient K is a value set to reflect the effect of the aperture ratio and relative plate thickness that is not considered in the formula in the aperture machining force P. The coefficient K is set to be smaller as the aperture ratio and relative plate thickness is larger, and the smaller the coefficient K, the upper limit is 1.0.
The press machine must choose one that can hold the flange at the appropriate pressure. During drawing, the flange part is held with a blank holder (wrinkle control plate) of the press machine, but if this pressure is too weak, wrinkles will occur if it is too strong, and cracking will occur. This pressure is important for flange molding, but the strength of the pressure depends on the material of the material, plate thickness, etc., so it is a good idea to choose a press machine with adjustable pressure.
In addition, when selecting a press machine, it is necessary to be careful that there are dimensions that can be attached to the mold, that there is a mechanism that can peel off the part attached to the punch, and that there is an interval between the punch and the die that can take out the part after the drawing is completed.
(5) Precautions before actual processing
After the above process, we will proceed to actual processing, but there are a few points to note before that.
First, you need to make sure that the materials specified or selected by the order can be squeezed according to the design. The characteristics of materials related to drawing include tensile strength, yield point, elongation, and hardness, but when considering the drawing workability, the processing hardening coefficient (n value) and the Rumford value (r value) of the material are often referred to. The r value indicates that when the plate material is stretched in the longitudinal direction, it is easier to shrink in the shorter hand direction than in the thickness direction.
In addition, it is also a problem whether to use lubricating oil and which lubricating oil to use during drawing. Lubricating oil makes the ground surface of the blank and die slippery when the blank is pushed in with a punch. Therefore, without lubricating oil, friction between blanks and dies can cause breaking, seizure, quenching, etc.