The forging process of butt-welded flanges generally consists of the following procedures, namely, selecting excellent billets for blanking, heating, forming, and cooling after forging. The forging process methods include free forging, die forging, and membrane forging. When producing, choose different casting methods according to the quality of the forgings and the production batch.
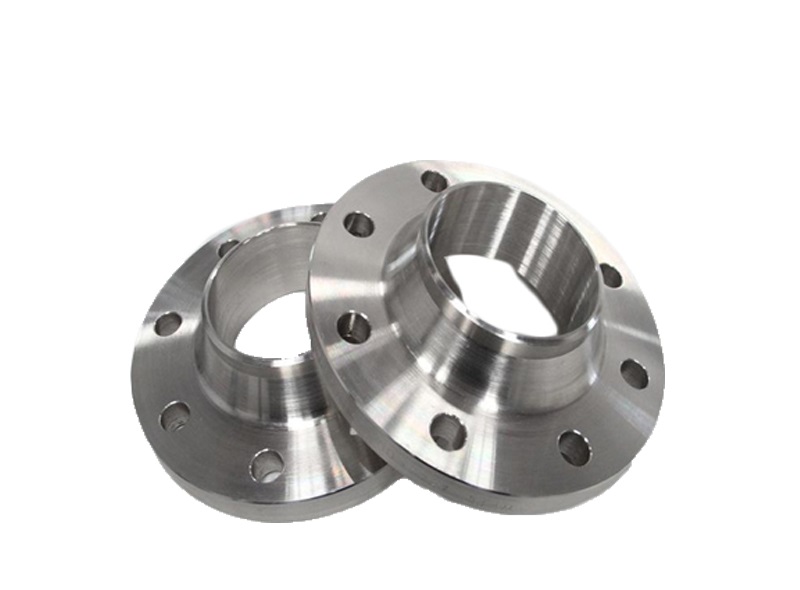
Butt-welded flanges are mostly used in environments with relatively mild media conditions, such as low-pressure non-purified compressed air and low-pressure circulating water. Its advantage lies in its relatively low price. The sealing surface of the butt welding flange can be divided into three types: smooth, concave and convex, and tongue and groove. Smooth butt-welded flanges have a wide range of applications, and the other two methods of butt-welded flanges are also relatively more in use. The butt welding flange has a reasonable structure, high strength and rigidity, and can withstand various harsh environments such as high temperature and high pressure, repeated bending and temperature fluctuations, and it will not reduce the sealing performance.
Butt-welded flanges are mostly used in environments with relatively mild media conditions, such as low-pressure non-purified compressed air and low-pressure circulating water. Its advantage lies in its relatively low price. The sealing surface of the butt welding flange can be divided into three types: smooth, concave and convex, and tongue and groove. Smooth butt-welded flanges have a wide range of applications, and the other two methods of butt-welded flanges are also relatively more in use. The butt welding flange has a reasonable structure, high strength and rigidity, and can withstand various harsh environments such as high temperature and high pressure, repeated bending and temperature fluctuations, and will not reduce the sealing performance.
Butt Weld Flange: The butt welding flange is similar to the sliding flange, but the thread of the hole. Its main advantage is that it can be assembled without welding, in the ordinary interpretation of atmospheric temperature in low-pressure service use and extremely explosive areas, welding creates a danger.
Slip On Flange: The slide on flange has a lower hub because the pipe enters the single flange before welding. It is welded inside and outside to provide enough strength to prevent leakage. Sliding flanges are matched with boring pipes with slightly larger outer diameters. They are better than the welding of neck flanges, because the initial cost is lower for many users, but the final installation cost is probably not comparable, because the number of welded neck flanges is less.
Lap flange: The lap flange is actually exactly the same sliding flange, unless it is a radius between the hole and the flange race. It is necessary for the radius to have the flange to accommodate the end of the lap stub. Usually, the lap flange and the lap stub end mating together will assemble the system.
The socket butt weld flange is a similar slid on flange, unless it has a hole and a counter hole size. The counter hole is slightly beer than the O.D. pipe to match, so that the pipe is inserted into the flange similar to the slide on flange. The diameter of the smaller hole is matched with the same pipe with the same ID. The restriction is a built-in hole that stays at the bottom as a shoulder sleeve designed for pipes. This eliminates any flow restrictions when using socket weld flanges.
At present, butt-welded flanges are widely used and popularized in pipe fittings, because the scope of application and use environment are different, so they need to be used in corresponding ways and methods.