Flanges mean buttoots, edges, and brims, but in industrial terms, they refer to fittings connecting the two pipes. Flanges are widely used in various places such as mechanical parts, electronic components, and building parts, but I think many people do not know how they are actually molded.
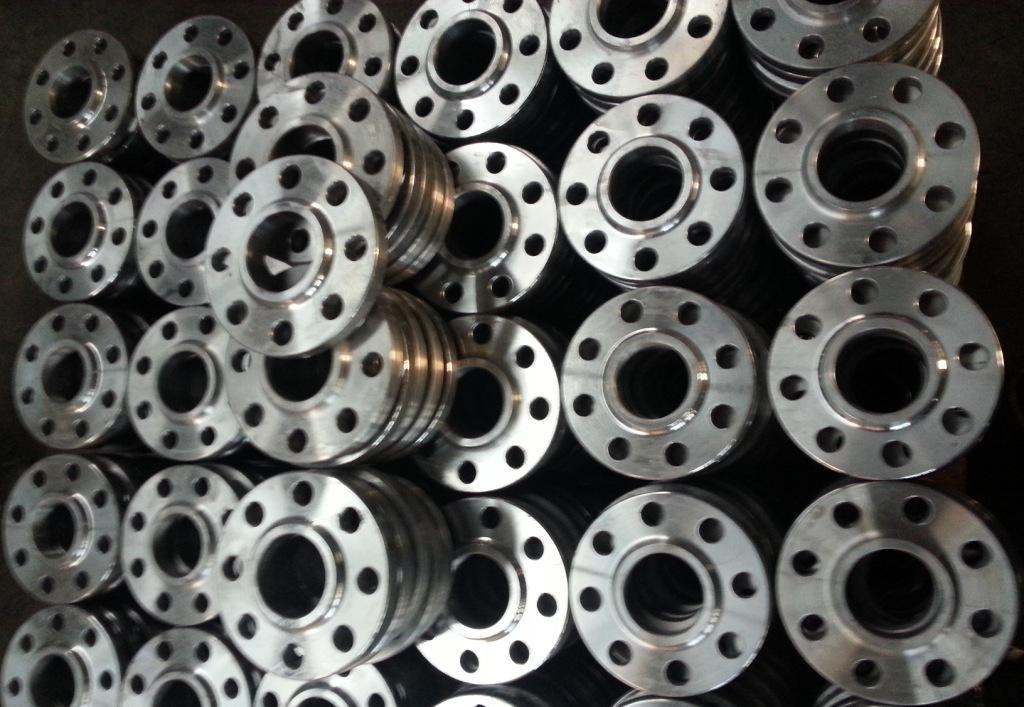
Therefore, in this article, we will explain in detail how to machine flanges. In addition, we will introduce many processing cases, so please refer to it when requesting flange processing.
Method of Flange Processing
Flange molding methods include a processing method that is cut out by NC lathes, machining centers, etc., and a processing method in which sheet metal is squeezed or bent by pressing machine. In addition, flanges are often molded by manufacturing only flanges separately and welding.
- Lathe processing
Lathe machining is a method of performing processing such as outer rounding, surface milling, turning, drilling, parting off, threading, etc. by applying a tool to a rotated workpiece using an NC lathe or the like. It is mainly used when cutting out disk-shaped flanges from rod-shaped materials.
However, the machining geometry due to lathe machining must be continuous rotational symmetry. Therefore, for flanges with complex shapes, additional work such as machining centers may be required after lathe machining.
- Cutting
Cutting is a method of drilling, drilling, milling, milling, threading, reming, etc. by applying a tool that rotates or straight-acting on a fixed workpiece using a machining center or the like. It is mainly used when square flanges that cannot be machined with lathes or when additional work with complex shapes that are difficult for lathe machining is required.
- Sheet metal processing
The method of forming flanges from sheet metal is to use presses for drawing and bending. Drawing is used for shapes such as containers and pipes, and bending is used when forming flanges into shapes such as plates.
- Drawing
In drawing, as shown in the figure below, a material (blank) is placed on the lower mold (die) and the flange part is suppressed with a blank holder. Then, the upper mold (punch) presses the blank and molds the container part and the flange part at the same time.
- Bending
On the other hand, in bending, flanges are molded by processing methods such as V bending that can be bent at various angles, L bending that bends one place at an angle of 90 degrees, and U bending that bends two places at an angle of 90 degrees.
The features of these three types of bending are mentioned first, V bending allows free bending, which can change the angle of the bend by adjusting the clearance between the die and punch, and the ability to transfer the shape of the punch die or push the punch to compress the blank. On the other hand, in L-bends and U-bends, the clearance is always kept constant. However, if the force of the pad is weak, blanks may be drawn in the punch direction in L bending, and the flatness of the bottom of the container shape may be unstable in U bending.
- Flange type
Flanges molded by sheet metal are divided into three types: straight flanges, shrink flanges, and elongation flanges in terms of material flow conditions.
A straight flange is a flange when the line is straight. In the drawing process, the machining line of the flange part becomes a straight line by the square cylinder drawing shown in the figure below, and this flange part receives tensile stress in the bending direction. On the other hand, in bending, the flange when simply bending and forming a plate etc. becomes a straight flange, and stress does not work on this flange part.
A shrink flange is a flange when the wire is curved outward. In the drawing process, the pull stress is received in the bending direction, and compression is received to the flange in the bending direction and the right angle direction.
On the other hand, in bending, compression in the bending direction and the right angle direction is received on the flange part.
When it comes to shrinking flanges, the bending process must take into account the effect of compression in advance and make the shape of the flange part an open fan shape. In the drawing process, the flange is mainly formed by pressing disc-shaped sheet metal, but in this case, the flange part is a fan shape before consideration.
In addition, shrinking flanges have the effect of thickening the flanges because a force to compress is applied to the flange. As a result, sagging and wrinkles tend to occur in the flange, so care must be taken.
An extension flange is a flange when the wire is curved inward. In drawing, compressive stress is received in the bending direction and tensile stress is received to the flange in the bending direction and the right angle direction. On the other hand, in bending, tensile stress in the bending direction and the right angle direction is received on the flange part.
When it comes to elongation flanges, as with shrinking flanges in bending, it is necessary to consider the effect of tensile stress and keep the shape of the flange part in a closed fan shape. In addition, as opposed to shrinking flanges, it is necessary to pay attention to the occurrence of cracks because the flange part has a thinning effect.