What is a Weld Neck (WN) flange and what are its advantages? What are their common applications?
Today, we show you the main characteristics of weld neck flanges, known in English by Weld Neck and more specifically, by its acronym (WN). Discover its applications, advantages, disadvantages and minimal parameters for its definition.
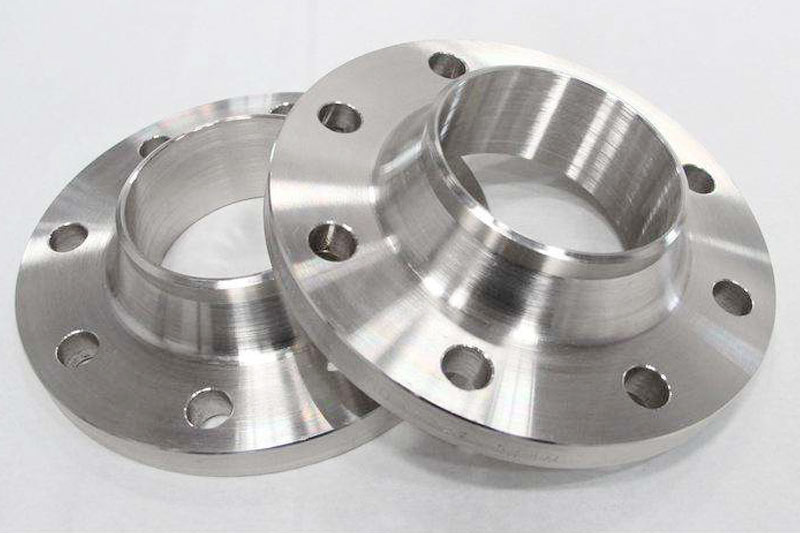
What is Flange?
A flange is an element that joins two components of a pipe system, allowing it to be disassembled without destructive operations, thanks to a circumference of holes through which connecting bolts are mounted. The flanges are those elements of the pipeline, intended to allow the union of the parts that make up this installation, whether they are pipes, valves, pumps or other equipment that is part of these installations.
Related Read: What is Socket Weld Flange?
What is Weld Neck Flange (WN Flange)?
Welding neck flanges are also usually known by their English name Welding Neck Flange. They are characterized by having a long conical neck.
Advantages
The long neck, and the smooth transition of its thickness, give this type of flange characteristics of strength that make it suitable for use in sectors where the pipes are subjected to deflection forces, as a result of the expansions and contractions of the lines.
How is it assembled?
The end of the flange is buttweld with the pipe, in the same way that two pipe ends are welded. This characteristic provides a conduit with a practically constant area, without the possibility of producing turbulence in the circulating fluids.
In addition, the butt weld between the WN flange and the pipe, also called buttweld in English, allows it to be inspected by radiographic or ultrasonic methods. These inspection tests give the WN flanges greater reliability and safety in use.
Lastly, the butt weld between the flange and the pipe has good fatigue resistance and does not induce local stress points.
Minimum data to define a WN flange
To fully define a WN neck flange, the following data will be required at least (the values shown in the table are indicated as examples)
Material | Norma | Face | Pipe diameter | Serie | Pipe Schedule |
A105N | B16.5 | RF | 6” | 300 | 80 |
WN Flange Recommended Use
The flanges with welding neck or Welding Neck (WN) are recommended for severe services, whether due to high temperatures, high pressures, because they are flammable, corrosive or toxic liquids, or in those services where leaks of any kind must be kept to a minimum.
Typical Applications
Lines for water, steam, oil, natural gas, refined hydrocarbons, condensates, fire networks, compressed air, etc. It is the type of flange used par excellence in the oil refining industry.
WN Flange Disadvantages
- Space: Due to its gradually reducing weld neck, weld neck flanges occupy more longitudinal space in the pipe to be mounted compared to other types of flanges. In some cases the available space is so small that a WN flange cannot be mounted.
- Man Hours: Due to the butt weld between the pipe and the weld neck of the flange, it is necessary to chamfer the end of the pipe. This increases the man-hours required to assemble, and forces abrasive tools to be used on the pipe, which generate sparks. This can limit the use of the WN flange in cases where the pipe is mounted in a process unit which is in service, or the pipe is contaminated inside with flammable products. In addition, to bevel the pipe it is necessary that it has an acceptable thickness.
- Price: WN flanges have more weight than other types of flanges and require more material in their manufacture, which increases their cost.