In this article, we will introduce basic knowledge of flange types, shapes, standards, materials, etc.
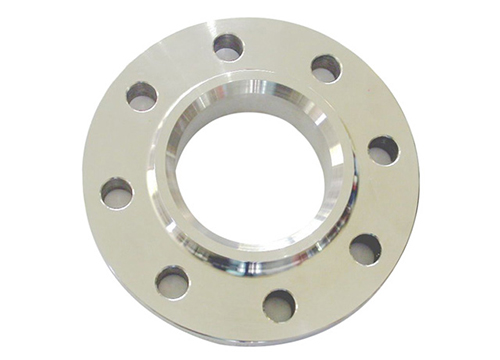
Flanges are a type of piping fitting, and flanges made of shaped steel, but this time I will focus on piping fittings. Flanges are used to connect pipes and valves in machines and plants. However, knowledge of standards, geometry, etc. is required for flanges to be properly joined and functioning.
What is a flange?
Flange refers to a power bar for joining the ends of a part to other parts. Basically, it becomes a thing in the shape of a circle, but the protrusion part for joining is often called a flange.
The flange has a hole in the center for passing the pipe, and in the part of the connecting part there is a hole for bolting.
Flange applications are basically used in piping. This is used to disassemble piping and make it easier to maintain the inside of the pipe, or to simplify assembly.
Piping is responsible for carrying fluid, but must be joined to prevent fluid from leaking. Therefore, there are many situations where the flange joint surface is sealed with a gasket (packing). Flanges also need strength to withstand internal pressures.
Flange Type
There are various types of flanges due to the difference in the connection method with the pipe.
The insert welded flange (slip-on flange: symbol SO) is a popular type of flange because the pipe is inserted into the hole in the center of the flange and the pipe is welded in two places: the upper surface of the flange and the inner diameter part on the opposite side.
The insert welded flange is divided into a “hub flange (SOH)” with a edge around the central hole and a plate-shaped “plate flange (SOP)” depending on the shape.
The insert welded flange does not need to have a beating, and while it has the advantage of making construction easier, it is not suitable for high-temperature piping because it is inferior in strength.
Socket welded flange (socket weld flange: symbol SW) is a type with a body part (step) provided in the hole in the center of the flange. Insert the tube so that it hits the body part, and then weld the corner of the outer part of the pipe on the top of the flange.
As shown in the figure above, socket welded flanges (SW) differ from inserted welded flanges (SO) that weld corners to two parts of the pipe top and inner diameter, so there is no risk of adverse effects on the sealing surface of the flange.
Socket welded flanges are often used for connecting small diameter piping. On the other hand, since there are few welding points, it is not suitable for high-temperature and high-pressure piping.
Butt welded flanges (weld neck flanges: symbol WN) are welded by applying a bee processing to the butt part with the tube.
Butt welded flanges are strong against thermal stress and vibration, making them suitable for high temperature and high pressure applications. Another advantage is that the inner surface can be finished smoothly.
- Matched Flange (Loose Flange / Wrap Joint)
The combination flange (loose flange / lap joint: symbol LJ) is a type that, as shown in the figure above, the pipe is joined and welded with the “stub end” which is a piping joint with a collar, and the collar part of the stub end is hooked to the joining surface of the flange.
The stub end is only hooked to the flange, so it can be rotated freely. This feature allows position adjustment to match the bolt hole position of the flange to be joined.
Used flanges are often used for joining flanges to pipes that cannot be welded, and for piping under low temperature, low pressure, and hazardous environments.
The screw-in flange has a tapered threaded flange inner diameter, and it is a type that screws and joins the tube with the tapered thread.
Threaded flanges do not require welding, so they are suitable for places where fire is not available. It is also ideal for room temperature, constant pressure and hazardous fluid applications. However, since the pipe and flange are joined by screws, sealing characteristics are poor.
Flange Shape (RF, FF, MF, TG, RJ)
This section explains the shape of the gasket face (joint surface) of the flange. Flanges are available in a wide variety of shapes, and depending on the application and type of gasket used, it is necessary to use them properly.
- RF
RF is a flange called “flat seat” or “raised face”, with a flat seat inside the bolt hole. Among the flange shapes, there are many scenes that are most adopted.
RF is classified as a “large plane seat” with a seat near the inside of the bolt hole and a “small plane seat” with a small seating area.
- FF
FF is a type of flange called “front seat” or “flat face”, in which the entire flange joint surface is finished face-to-face.
In general, it is joined with the packing so that there is no leakage of fluid through the tube.
- MF
MF is a type called “indentation” or “mail and female”, and refers to the type that fits each other together by a male “mail seat (MF-M)” with convex flange joint surface and a female “Female seat (MF-F)” with a concave female.
The MF type is used when you want to accurately center the connections between flanges.
- TG
TG is a type called “groove”, “tongue and groove”, and it is a type that is attached and joined with a thing with a groove in the flat seat and a thing with convexness in the plane seat.
The grooved thing is called the groove seat (TG-G) and the convex one is called the “TNG seat (TG-T)”.
Since TG can take a large surface pressure, it is used in hazardous fluids and vacuum piping where airtightness is important.
- RJ
RJ is a type called “Ring Joint Face” in which grooves for ring joint gaskets are provided on the joint surface of the flange.
Ring joint gaskets are made of metal, have excellent sealing properties due to wire contact with grooves, and have the ability to withstand high temperature and high pressure. In addition, the shape of the RJ has the advantage that the seal surface is in the groove and does not expose, so there is little damage to the seal surface.
Flange Pressure Temperature Reference (PT Rating)
“Pressure-temperature reference” and “P-T rating” are standard tables that provide the appropriate nominal pressure and material in relation to the temperature of the fluid and the maximum operating pressure.
Flanges must be shaped and materialed appropriately, depending on piping and fluid conditions. When the fluid is at what °C, how much pressure can be used is classified by symbols such as “5K and 10K~”, which is called “nominal pressure (rating)”.
Nominal pressure is also specified for JPI flanges and ANSI flanges, which are classified as “Class 150/ Class 300~” rather than K symbols.