What do you know about SW Flanges (Socket Weld Flanges)? What applications are they suitable for? How is this flange assembled?
SW flanges offer an excellent solution for small diameter pipes, characterized by a seat on which the end of our pipe rests. This configuration has a number of advantages but it also has a key drawback in its assembly. Did you know it?
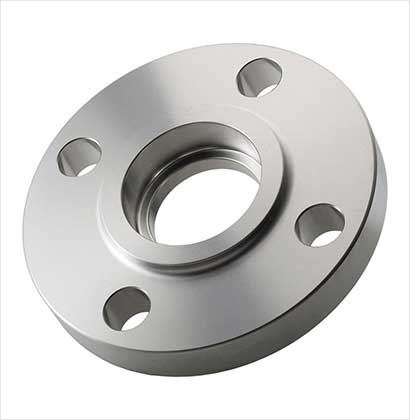
What is Flange?
A flange is an element that joins two components of a pipe system, allowing it to be disassembled without destructive operations, thanks to a circumference of holes through which connecting bolts are mounted. The flanges are those elements of the pipeline, intended to allow the union of the parts that make up this installation, whether they are pipes, valves, pumps or other equipment that is part of these installations.
What is Socket Weld (SW) Flange?
Weld seat flanges are also usually known by their English name Socket Weld Flange. They are characterized by having a seat on which the pipe rests, of the same diameter and thickness.
How is it assembled?
The flange cavity is fillet welded to the pipe, in the same way that two socket pipe ends are welded. This characteristic provides a conduit with a practically constant area, without the possibility of producing turbulence in the circulating fluids.
In addition, fillet welding, although it cannot be inspected by radiography, it is compatible with the inspection of magnetic particles and penetrating liquids.
Finally, it should be noted that this type of assembly does not require beveling the ends of the pipe, thus reducing assembly times and costs with respect to the WN flange.
Minimum data to define an SW flange
To fully define an SW seat flange, the following data will be required at least (the values shown in the table are indicated as examples)
Material | Norma | Face | Pipe diameter | Serie | Pipe Schedule |
A105N | Bl 6.5 | RF | 1” | 300 | 40 |
SW Flange Advantages
Socket Weld flanges need little longitudinal space in the line to be assembled and, because the weld is fillet, does not require the preparation of the pipe, reducing assembly times.
SW Flange Recommended Use
Socket Weld or Socket Weld (SW) flanges are recommended for services where internal welding operations are particularly difficult. This type of construction has the same static resistance as a slipon flange, but performs up to 50% better under fatigue.
Typical Applications
They are used in a wide range of fluids from water lines, condensate, steam, oil, gas, fire networks and compressed air and a wide range of pressures. They can only be used in small diameters, less than or equal to 2 “NPS (50)
SW Flange Disadvantages
- Sizes: Can only be used in reduced sizes, up to 2 ‘
- Welding work: Welding a socket flange requires some certainty and knowledge of practice. When we weld this pipe, it is necessary to insert the pipe as far as it will go and then move it about 1.6mm. The purpose of this displacement is to reduce the residual stress that occurs at the root of the weld during solidification of the filler metal.
- Corrosion: Due to the small space that must be made to avoid residual stress, corrosion can occur in the connection, especially in stainless steel systems where corrosive fluid can find its way into this connection